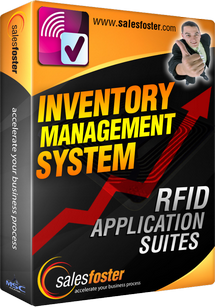
SalesFoster
RFID Series:
Inventory Management System
Although many companies are now using sophisticated Warehouse Management Systems integrated with Supply Chain Systems, Enterprise Systems, and Electronic Data Interchange (EDI), the movement and tracking of goods through the manufacturing and supply chain process is still a complex procedure which is difficult to manage. In many instances, the goods being distributed to the retailer must go through one or more third party distribution processes, before they reach their final destination.
Currently, most material tracking systems employ two-dimensional
barcodes that must be close to and within the "line of sight"
of the barcode reader. This requires manual scanning or a conveyor-like
process to position the barcode and scanner. Barcodes can run
the risk of getting wet or scratched due to mishandling or a
harsh environment, which often prevents accurate reading by
the scanner. Manual intervention is labor intensive, costly,
and error-prone. In addition, scheduled scanning or manual methods
cannot ensure the inventory remains up-to-date, due to oversights,
errors, and internal shrinkage.
With SalesFoster's RFID
solution, inventory can be updated in real time without product
movement, scanning or human involvement. Our fully automated
system allows inventory status to be determined, and shipping
& receiving documents to be generated automatically. The system
could also trigger automatic orders for products that are low
in inventory.
Benefits of using SalesFoster RFID Inventory Management
Whether tracking inventory in warehouse or security access, there is a clear need for a fully automated data capture and analysis system that will help you keep track of your valuable assets and equipment. ...
|
|